

(SNL-NM), Albuquerque, NM (United States) Sponsoring Org.: American Inst. Publication Date: Research Org.: Sandia National Lab. Volpe National Transportation Systems Center Department of Transportation, Cambridge, MA (United States).Sandia National Labs., Albuquerque, NM (United States).This paper documents the strain fields measured during the AANC tests and successfully correlates the results with analytical predictions. These test results have been used to evaluate the accuracy of the analytical models and to support general aircraft analysis efforts.
#Lap splice adhesive on aircraft skin#
One-hundred strain channels were used to monitor five different lap splice bays including the fuselage skin and substructure elements. Fuselage pressurization tests have also been conducted at the FAA`s Airworthiness Assurance NDI Validation Center (AANC) to obtain strain gage data from select locations on the FAA/AANC 737 Transport Aircraft Test Bed. Research on WFD has been performed both experimentally and analytically including finite element modeling of fuselage lap splice joints by the Volpe Center. One area of research involves the understanding of a phenomenon known as ``Widespread Fatigue Damage`` or WFD, which refers to a type of multiple element cracking that degrades the damage tolerance capability of an aircraft structure.

#Lap splice adhesive on aircraft crack#
Other effects, such as temperature and potential, as well as the impact of the environment on fatigue crack growth have also been studied.The Federal Aviation Administration Technical Center (FAATC) has initiated several research projects to assess the structural integrity of the aging commercial aircraft fleet.
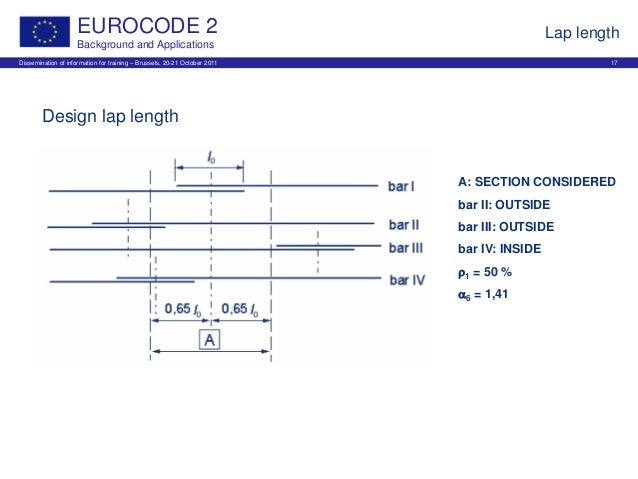
The extent and morphology of the attack in artificial lap joints has been compared to studies of corroded samples from actual aircraft. Laboratory studies have also included exposure tests involving artificial lap joints exposed to various simulated bulk and crevice environments. The statistically significant ions have been used to create a second generation solution. Additional tests have determined the relative importance of each of the detected ions in model solutions used for future predictive tests. Electrochemical analyses of the behavior of AA2024-T3 in these solutions gave corrosion rates of up to 250 microns per year (10 mpy). After determining the species present and their relative concentrations, the resultant solution was reproduced in bulk and electrochemical tests were performed to determine the corrosion rate. Measurements of pH of wetted corroded surfaces indicated an alkaline occluded solution. Over twenty different ions have been detected. CE analysis has been performed on over sixty corrosion product samples removed from both civilian and military aircraft. Capillary electrophoresis (CE) is used to identify the ionic species contained in corrosion product samples removed from fuselage lap splice joints. A protocol for collecting and identifying the chemistry of airframe crevice corrosion has been developed. The objective of this work is to develop a laboratory corrosion test protocol to identify the chemistry to which lap joints are exposed and to develop a model of the corrosion within the joints. Fuselage lap-splice joints are a particularly important structural detail in this regard because of the difficulty associated with detection and measurement of corrosion in these occluded regions. Determination of the Corrosive Conditions Present within Aircraft Lap-Splice Joints The complexity of airframe structure lends itself to damage resulting from crevice corrosion.
